Local Glass History
Between the 1770s and 1920s, at least seven glass factories were situated in or near the I-95/Girard Avenue Project area. Although only small sections of two factories have been directly impacted and excavated thus far, a remarkable amount of 19th-century American glass has been recovered. Most of the artifacts were found in privies just west of the glass factories, in neighborhoods where glassworkers, shad fishermen, and shipwrights resided. This exceptionally large assemblage of whimsies, free-blown and mold-blown hollowware, lacy pressed and pressed pattern glass, cut tableware, lighting, and bottles indicates the important role the glass industry played in defining the character and identity of this neighborhood.
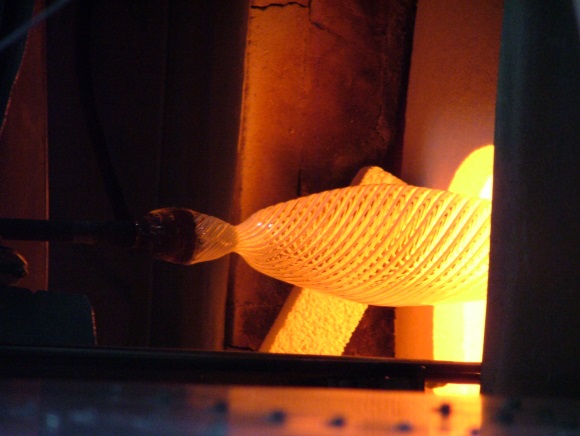
Glass is an extremely versatile material that is commonly used for various types of vessels, windows, and optics. We see it everywhere, but it is not easily defined. Glass is neither a true liquid nor a solid, but shares the qualities of both. It is often called an amorphous solid, and some scientists even consider it a fourth state of matter.
Making Glass
Glass is made by heating a mixture of dry ingredients, called batch, to a viscous state, then cooling it fast enough to prevent a regular crystalline structure. As the glass cools and becomes hard like a solid, the atoms become locked in a disordered state, like a liquid.
Glass batch has three main ingredients:
- Silica (silicon dioxide) found in sand, is the main component in glass. It requires very high heat to become viscous.
- An alkaline flux is needed to lower the melting point of the silica. In historical glass, the flux is usually soda ash (sodium carbonate), derived from marine plant ashes, or potash (potassium carbonate), made by burning bracken and trees.
- A stabilizer is needed because the first two ingredients are water soluble. Lime (calcium carbonate) is the most common stabilizer. Lead may also be used.
Batch is heated in a furnace to about 2400˚F. Broken glass, called cullet, is added to the batch to facilitate the melting process. Sometimes the glass itself is referred to as the “metal.” Other additives in the batch can change the properties and appearance of the glass, for example making it stronger, less reactive to heat, or opaque. There are thousands of different glass recipes.
http://www.youtube.com/watch?v=Q5NJ8jZ8M0k
This video was made at The Studio of The Corning Museum of Glass and shows how glass is made today. The batch was purchased premixed and heated in a computer-regulated furnace fueled by natural gas. Prior to these 20th-century advantages, glass factories acquired the raw materials and mixed the batch themselves. Factories in early America used wood for fuel before switching to coal. Variations in the quality of the glass itself and the accidental gray, tan, or pink tint often seen in “colorless” glass, are evidence of the challenges glassmakers faced.
http://www.youtube.com/watch?v=SWQzREycTyA
Coloring Glass
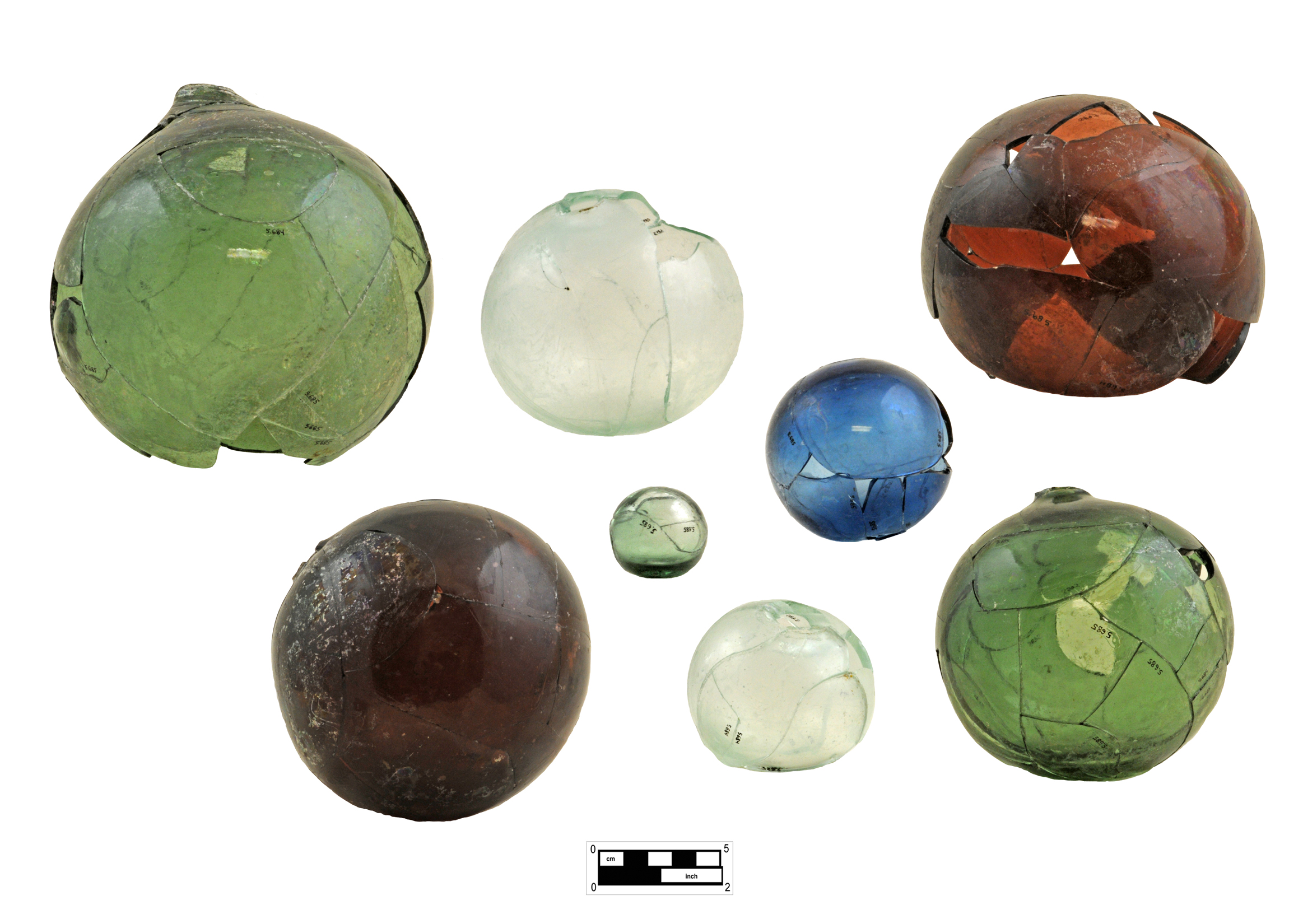
The color of glass is determined by metallic oxides in the batch. Naturally occurring iron in the sand causes various shades of green, amber, and brown. Decolorants, such as manganese dioxide, are used to take the natural color out of glass. However, it is very difficult to get all of the iron out of the sand. Common glass that appears colorless (clear) still has a subtle green or aquamarine tint visible in cross-section or in the thickest areas. “Artificial” colorants include cobalt for blue, manganese for amethyst, uranium for bright yellow and yellow green, tin for opaque white, and gold chloride for ruby red.
http://www.youtube.com/watch?v=M9e9_jcC-Ls
Free-Blown Glass
Free-blown glass is formed without the use of molds. The glassblower inflates the glass on the blowpipe and manipulates it with tools to make the desired form, such as a bowl, pitcher, or drinking glass.
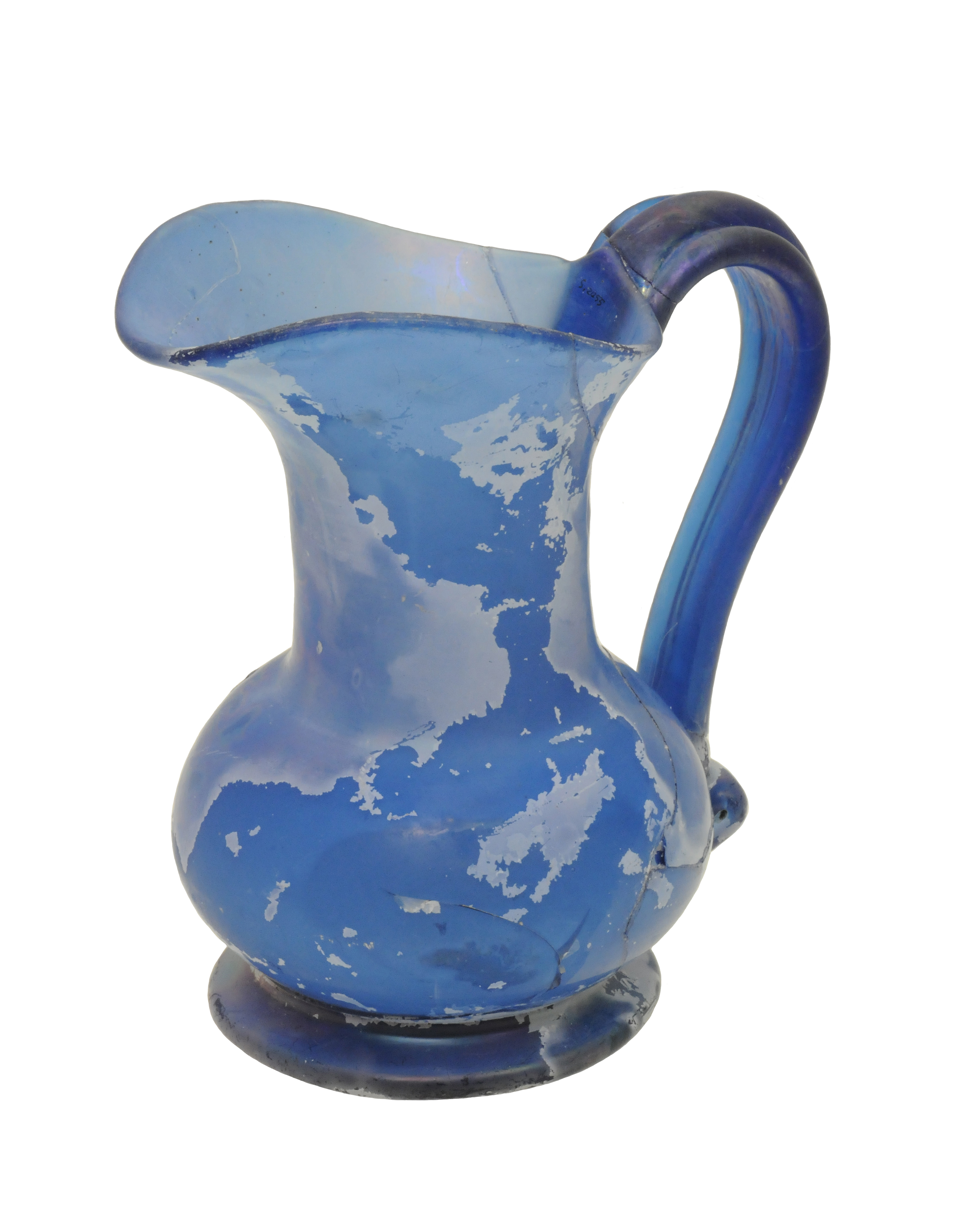
In a traditional glasshouse setting, the head glassblower of each team or “shop” is called the gaffer. To make a simple vessel, the gaffer or his assistant uses the blowpipe to collect a gather of glass from the pot in the furnace. He rolls it back and forth on a metal table (or extremely smooth stone) called a marver in order to shape and cool the gather. The gaffer blows through the blowpipe to form a bubble and begins to shape the glass. He may make it round by using a fruitwood tool, called a block, which looks similar to a cup on a long handle. Because the glass cools quickly and begins to harden, he must reheat the glass repeatedly at the glory hole, a reheating chamber at the furnace. While the glass is still on the blowpipe, he may continue building the object, by adding a stem and/or foot for example, as needed. In order to open the mouth of the vessel he is forming, his assistant helps to transfer the object to the punty, a long solid metal rod also called a pontil. Once the punty is attached to the bottom of the vessel, the glass is cracked off the blowpipe. He then opens the mouth of the vessel with a large tweezer-like tool called the jacks and may use additional tools to make the desired shape. He may apply handles or other attachments and hot decorative bits. When the piece is completed and cracked off the punty, it is immediately placed in an annealing oven to slowly cool; otherwise, the piece will break.
https://www.youtube.com/watch?v=n1dH_gm61jE&rel=0
https://www.youtube.com/watch?v=TSwCdnA-9uM&rel=0
Mold-Blown Glass
Glass may be blown, either by mouth or machine, into a wood, clay, or metal mold to give it form, decoration, or both. Using molds enables quick, uniform reproduction of specific shapes, sizes, and designs.
Dip Molds
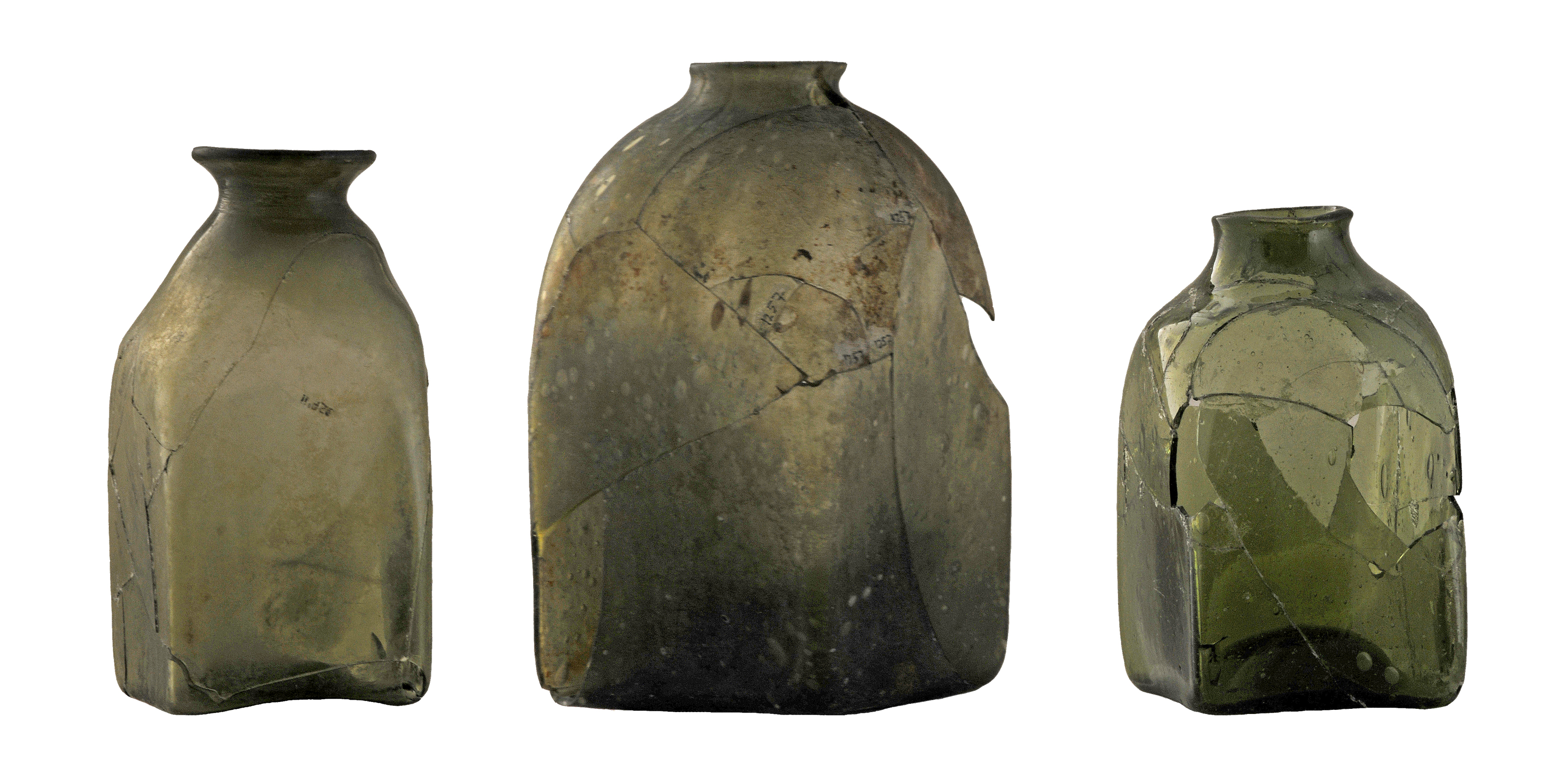
The simplest molds are one-piece dip molds. The glassblower lowers the gather of glass into the mold, inflates the bubble against the walls of the mold, and lifts the gather out. A dip mold may be used to shape the walls of a vessel, such as a square snuff bottle, but the shoulder and neck are finished by hand. Dip molds may also be used to impart a decorative pattern on glass.
Part-Size Pattern Molds
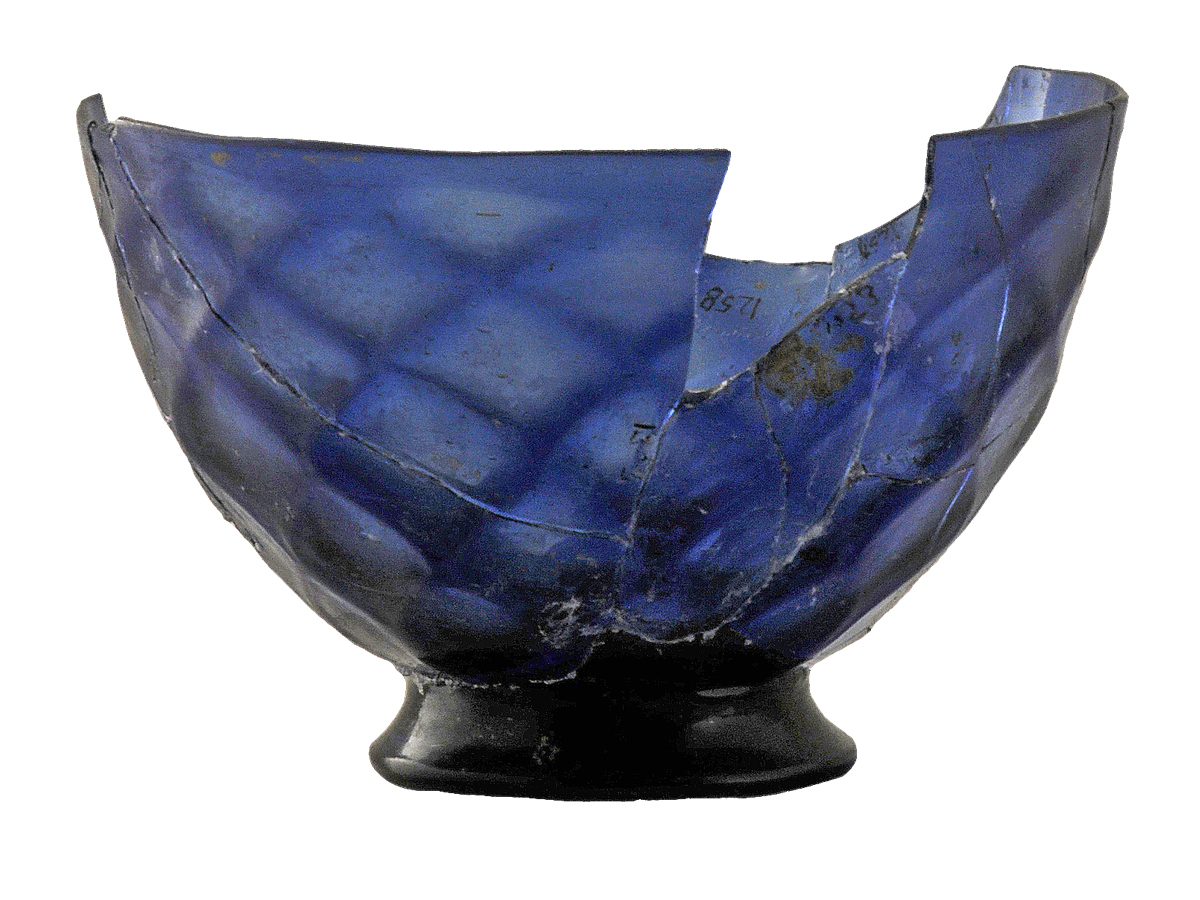
Dip molds and two-piece part-size molds are used to impart simple patterns, such as ribs or diamonds to the glass. The glassblower blows into a small mold to put the pattern on the glass. After removing the gather from the mold, the glassblower further inflates and manipulates the glass. The pattern becomes less distinct as the glass is expanded.
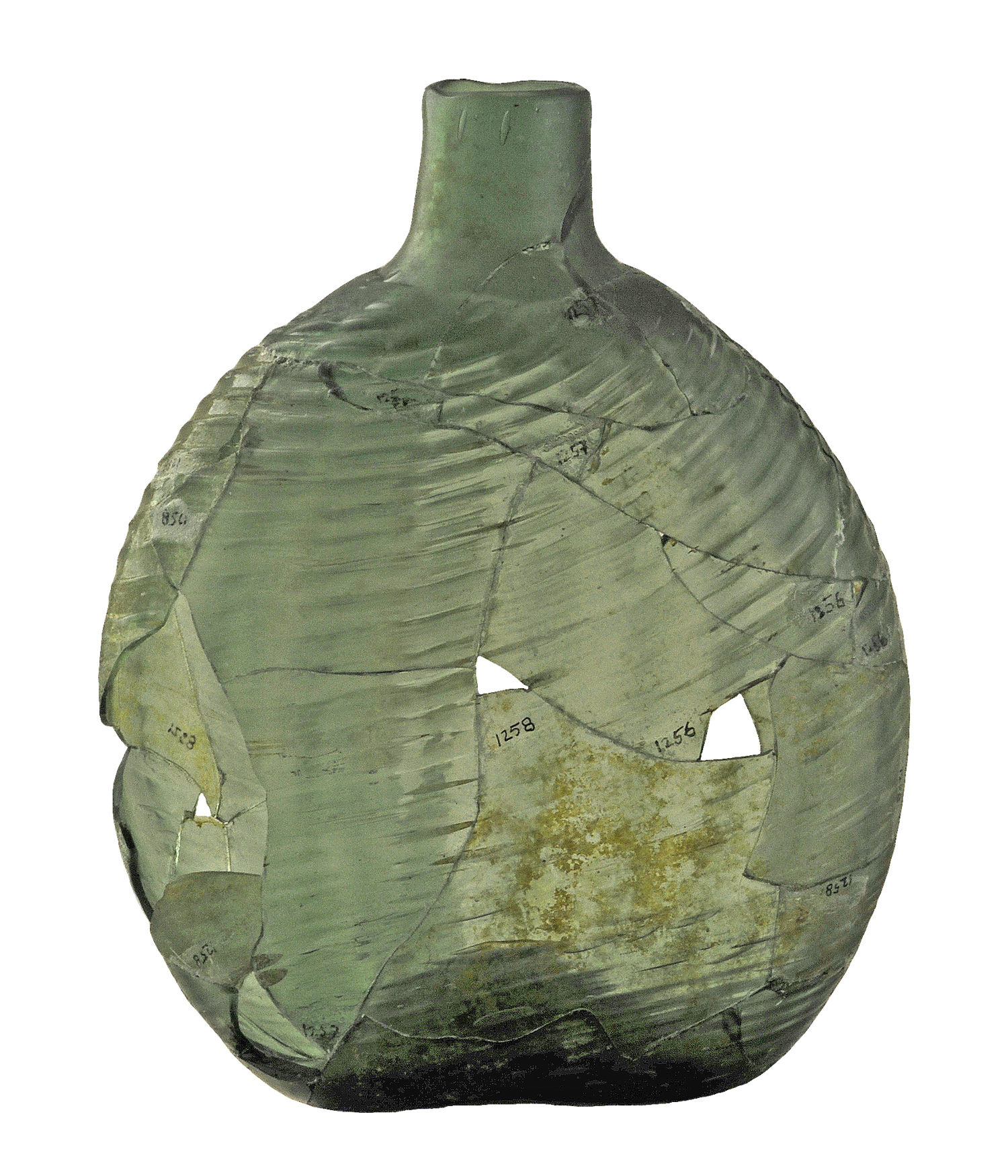
A swirl pattern is made by inflating the gather in a vertical rib dip mold, then twisting it. A “broken swirl,” sometimes seen on early American flasks, is achieved by creating a swirled rib pattern, then dipping the gather again to impose vertical ribs on the swirls.
Characteristics of Glass Blown in Part-Size Molds
Because they are further blown and shaped after being blown in the mold, pattern-molded objects may be asymmetrical or irregular in shape. The design formed by a part-size pattern mold is less distinct where the glass is more thinly blown. The contour of the pattern on the inside corresponds to the pattern on the outside. For example, the ridges of a diamond pattern that protrude on the outside of a vessel will also protrude on the inside. The seams of a two-part mold may follow the pattern and be difficult to identify on the object.
Full-Size Molds
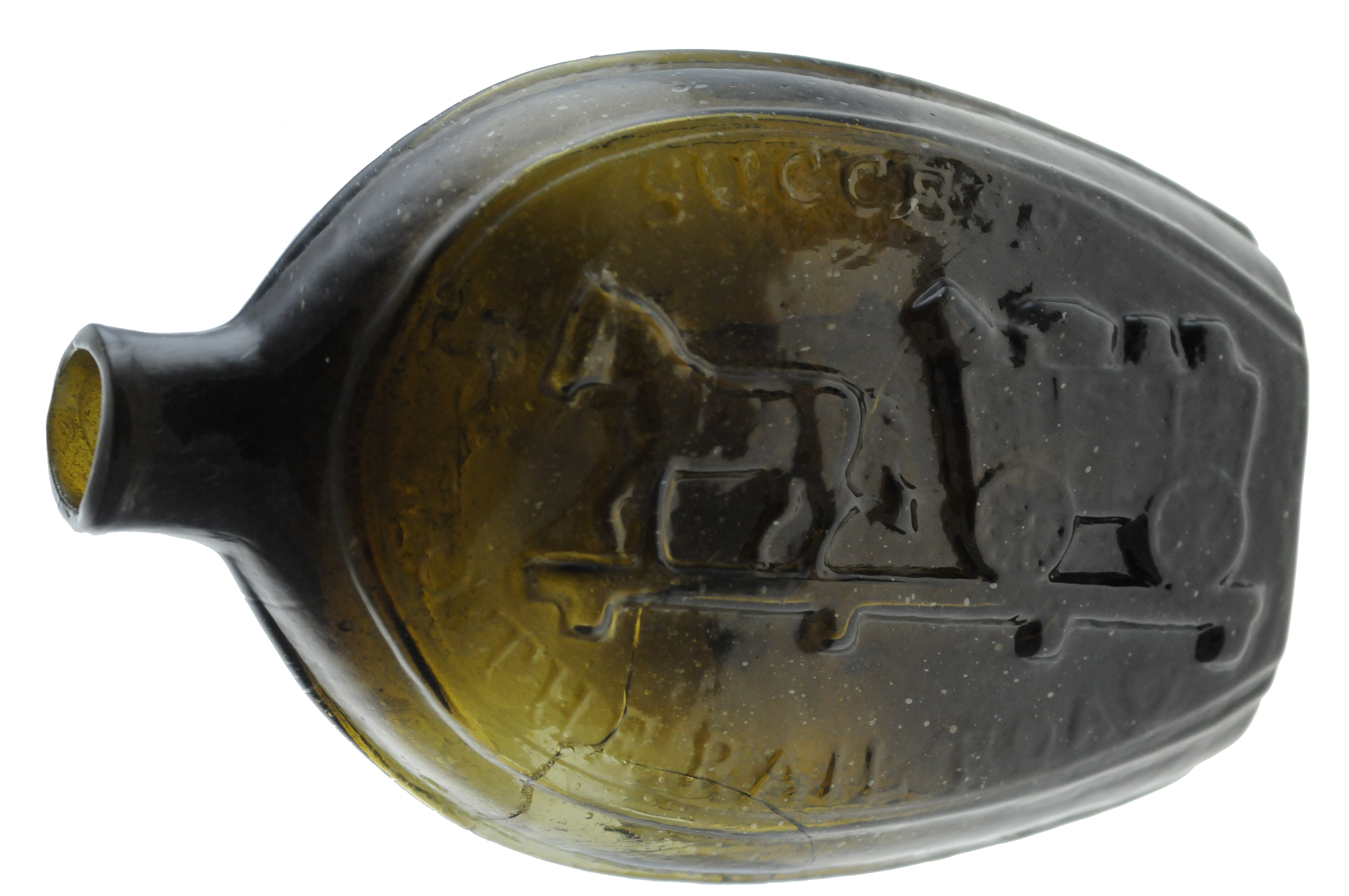
Glass may be blown into a full-size mold to give an object its shape and decoration. In the 19th century, many bottles and flasks were blown in two-piece full-size iron molds. This was an excellent means of ensuring consistent capacity and giving the container a complex embossed design. The body and neck of the bottle were formed in the mold and the glassblower finished the lip.
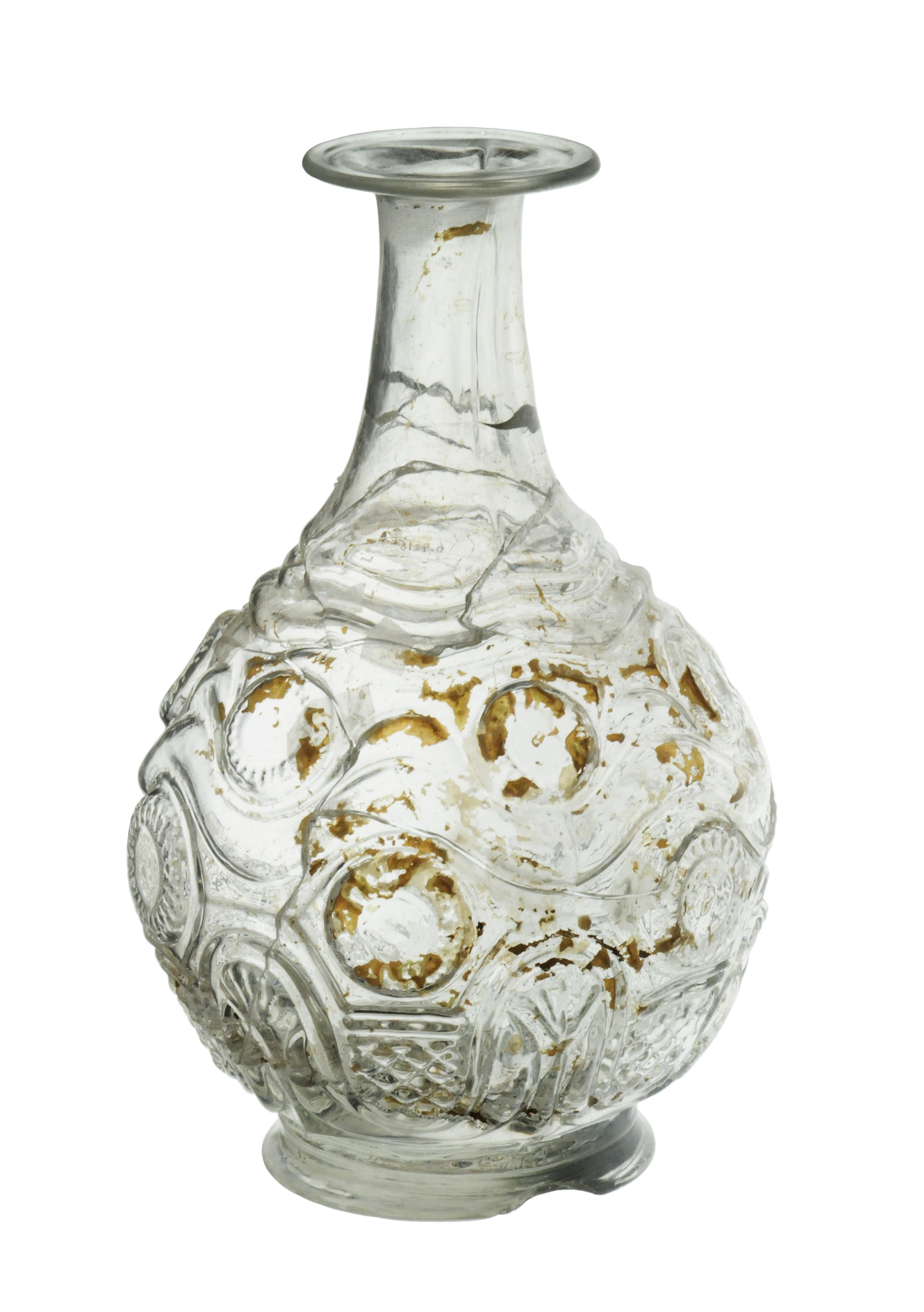
Blown three mold is the term used to describe glass blown into full-size metal hinged molds that usually have a base section and three vertical parts. After blowing into the mold to give the piece its basic shape, size, and decoration, the glassblower would manipulate the glass into the desired form. For example, the glassblower might blow into a decanter mold, then open out the mouth and add a handle to create a pitcher. This type of glass was very popular in America between about 1815 and 1835. The patterns often imitated cut glass designs. George and Helen McKearin’s American Glass, first published in 1941, includes a cataloging system for this type of glassware.
Characteristics of Glass Blown in Full-Size Molds
The embossed decoration created by blowing into a mold has parallel surfaces on the exterior and interior of the object. One should be able to feel the decoration on the interior as well as the exterior. Also, the decoration is usually smoother and lacks the crisp detail commonly seen on pressed or cut glass. Seam lines are often evident and reveal where the sections of the mold came together. By counting the seams, you can usually determine if the mold had two, three, or more parts. The surface of the glass may be slightly textured and it often lacks the glossy appearance of free-blown glass.
https://www.youtube.com/watch?v=-mJNmdvFkK8&rel=0
Pressed Glass
The concept of forcing glass into a mold to give it shape is an ancient idea, but tools specifically designed for this purpose developed gradually in the 18th and 19th centuries.
https://www.youtube.com/watch?v=gbhwS5FyToQ&rel=0
Plier Press
From about 1740 to 1900, a two-handled tool, sometimes called a plier press, was used to pinch glass chandelier drops, small stoppers, and toy cup plates.
Hand Press
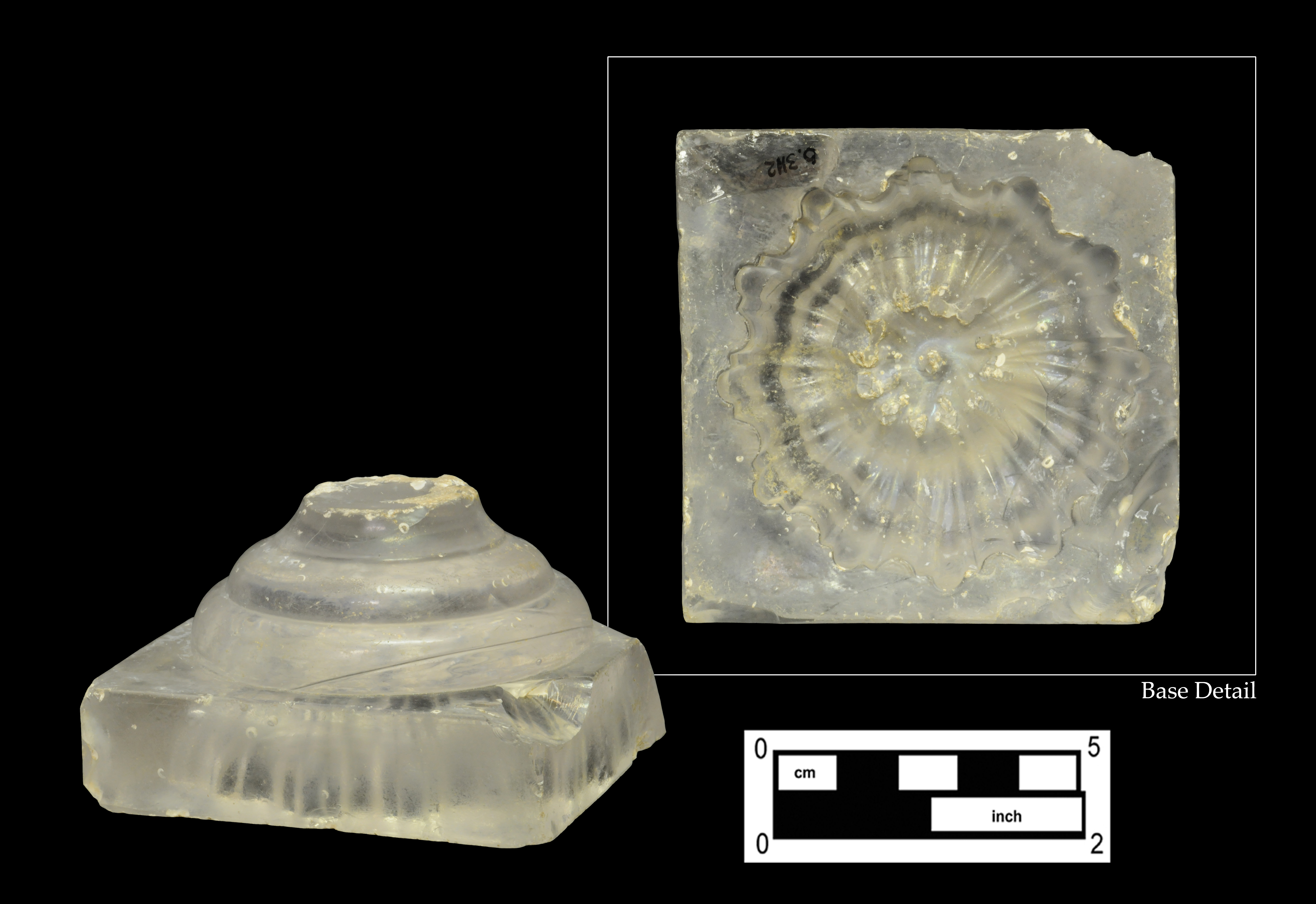
The hand press came into use in Europe around 1780‒85, but was not used in America until the 1810s or 1820s. Often used to make “feet” or bases for lamps, candlesticks, goblets, and other forms, hot glass was lowered into an open mold and pressed into the form with a hand-held plunger that imparted a decoration on the underside. Today such bases are sometimes called “lemon-squeezer” bases because the plunger usually had a ribbed pattern, making the underside of the glass base look somewhat like the underside of a lemon squeezer. Use of the hand press continued until about 1840 and overlapped with the development of more sophisticated pressing techniques.
Bench Press
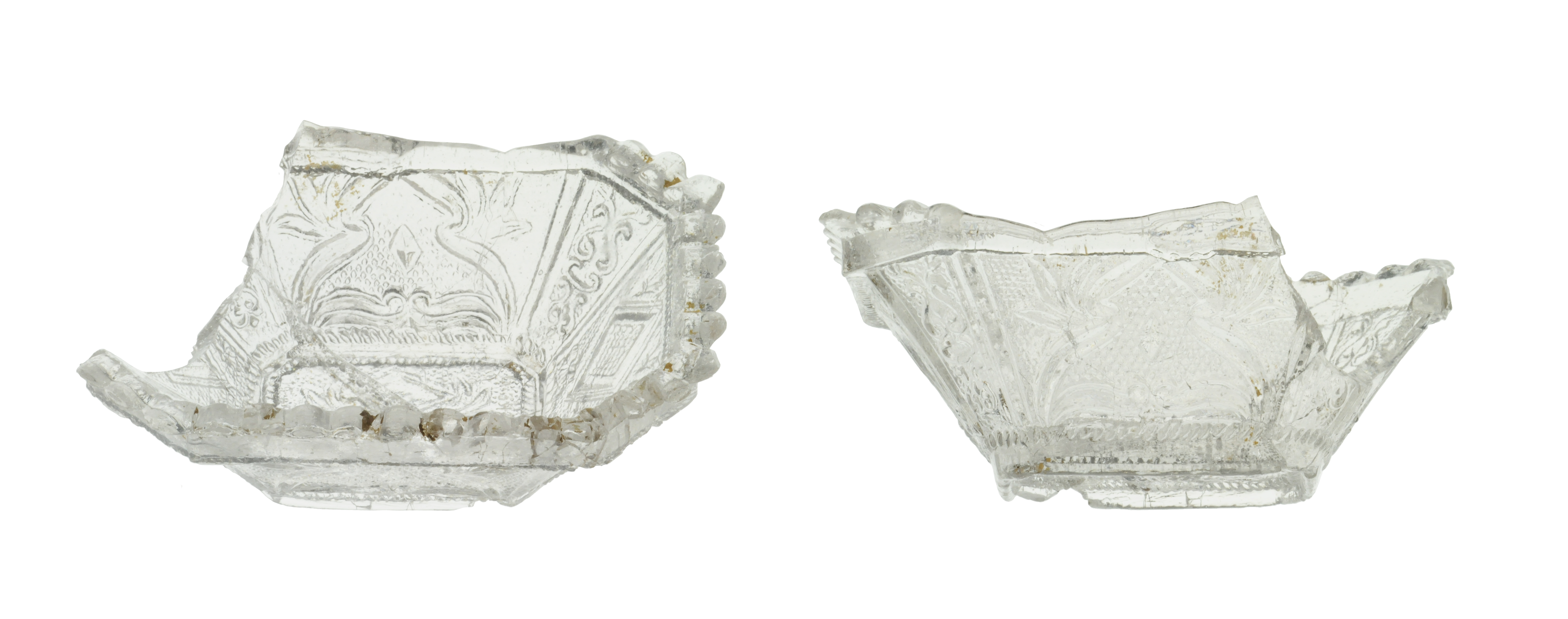
The bench press, invented around 1825 or 1826 and used until about 1850, was the first pressing mechanism to use a lever to force glass into a mold. The term “bench press” is a 20th century term used to differentiate this mechanism, which had to be mounted to a table or bench, from the free-standing machine press. Small forms such as furniture knobs, salts and cup plates could be made in the bench press. Union Glass Works in Kensington was one of the first companies to use this technology.
Free-standing Machine Press
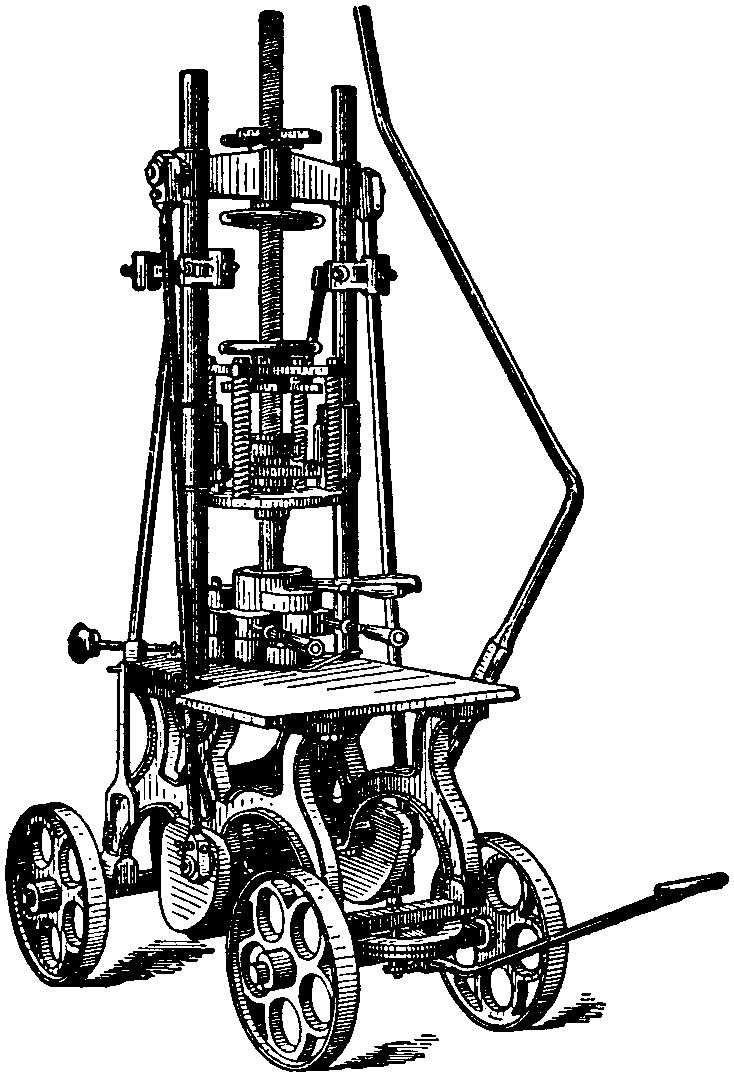
The free-standing machine press shortly followed the invention of the bench press. Through the use of a large screw or side arm, the machine press could provide greater vertical pressure and improved alignment of the plunger and the mold, so larger articles could be made.
The bench press and machine press could be operated by two relatively unskilled laborers, one to gather the glass and lower it into the mold, and the other to cut off the gather of glass, close the mold, and pull the lever down to force the plunger into the mold. Another assistant, often a boy, would then carry the finished piece to the annealing oven, where it slowly cooled.
Much pressed glass dating from the mid-1820s to about 1840 has elaborate stippled decoration and is therefore called “lacy pressed” glass. The fancy patterns were designed to hide surface imperfections caused by the pressing technique, as well as the shear mark created when the glass was cut off the gathering iron. When hot glass is pressed into a metal mold, the mold is colder than the glass and causes tiny ripples, called chill marks, on the surface of the glass.
Characteristics of Pressed Glass
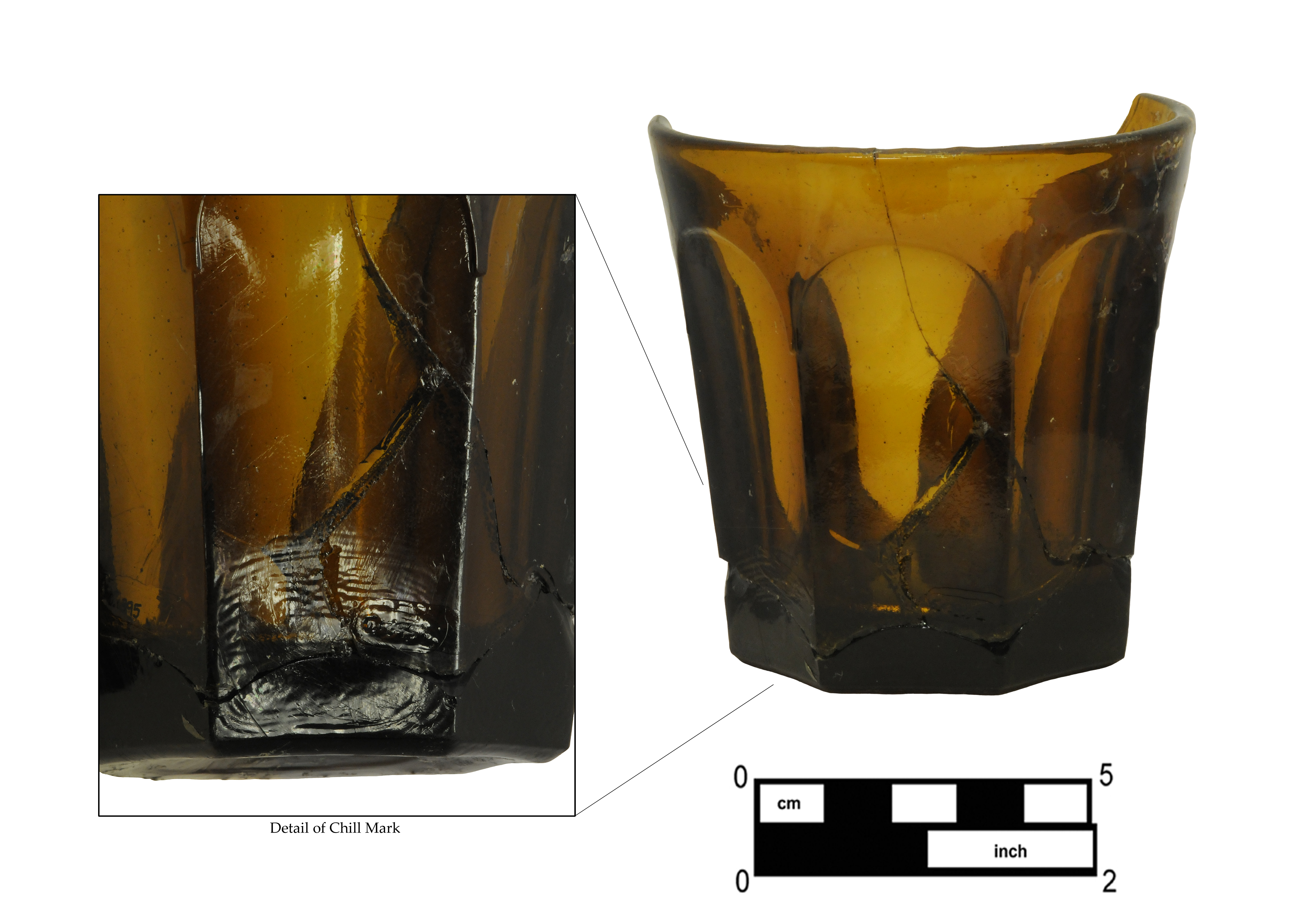
Unlike mold-blown glass, one surface of pressed glass usually carries the decoration and the opposite side is very smooth. Except for very shallow open forms, press molds have multiple parts. Seam lines are often apparent where the sections of the mold joined. On some objects, the seams protrude and are quite sharp because the glass was forced into thin crevices between the mold sections. In other cases, the seams may be well integrated into the design or fire polished (slightly heated) to make them smooth and less visible. Also, in determining if an object was pressed or cut, generally the cut decoration will be sharper and have slight irregularities in the design. Molded glass usually has a duller, somewhat textured surface compared to the glossy surface of free-blown glass or polished cut glass.
All of the illustrated artifacts were recovered from the I-95/Girard Avenue Project area in Philadelphia. Videos presented courtesy of The Corning Museum of Glass.